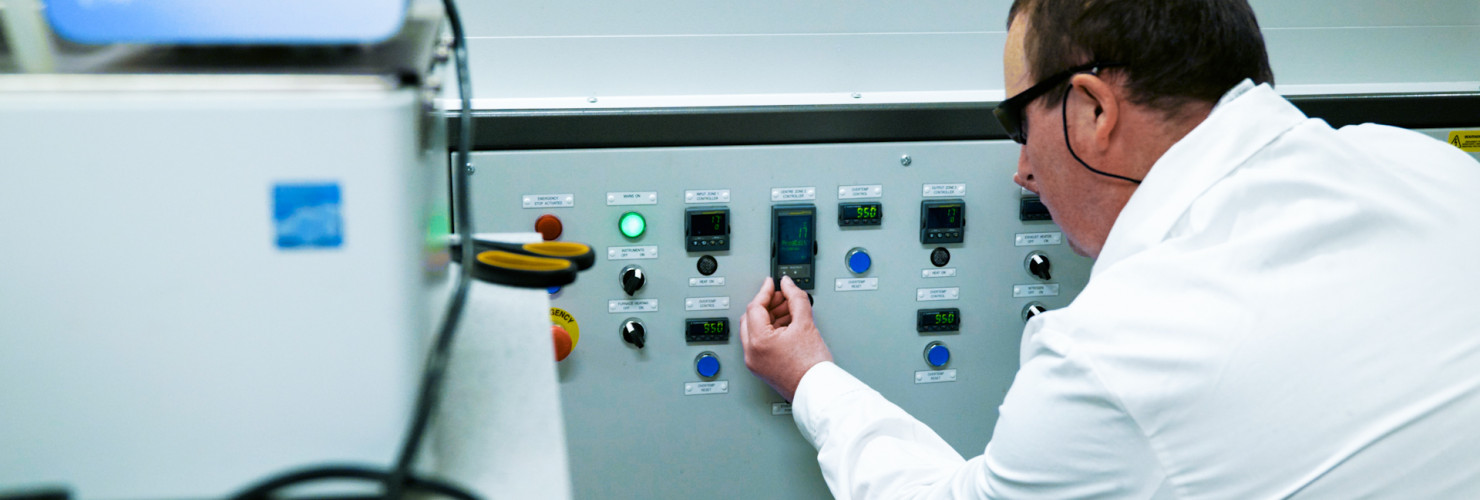
BDC wins 3 new UKRI funded projects which aim to enhance UK sustainable biomanufacturing
We have been awarded three new feasibility projects to collaborate with industry to develop and improve sustainable biomanufacturing in the UK. This joint investment is funded by the Biotechnology and Biological Sciences Research Council (BBSRC), Engineering and Physical Sciences Research Council (EPSRC), Innovate UK and overall will support 34 feasibility studies across the UK.
Our projects include:
Enzyme-based process for sustainable fertiliser from poultry manure with Lohas Recycling Limited and HarperAdams University (HAU).
Lin Lianying from Lohas Recycling explains;
It is an exciting time for Lohas Recycling. We are developing a brand-new patent pending enzyme-based process that can improve the current organic fertiliser manufacturing process effectively, reduce the reliance on natural gas, and improve food production with lower cost. By working with the Biorenewables Development Centre and Harper Adams University we will confirm the viability and sustainability of the new process by testing different operational conditions for producing safe and stable organic-based fertiliser from poultry manures, e.g. temperature, application rate and time.
Organic agricultural waste, such as livestock manure, contains valuable nutrients for plant growth. Poultry manure, with its blend of nutrients, is a perfect feedstock to manufacture organic-based fertiliser that is suitable for a wide range of crops, leafy plants and vegetables. However, without the effective and sustainable technology and process to manage and treat the poultry waste, the bio-based material risks bringing negative environmental impacts, such as ammonia emission, GHG emission and river pollution.
Previous work has been done on processing the poultry manure from a number of farms in England and Mid Wales, including broiler farms and egg farms. The output from the enzyme-based process has been tested for its safety (absence of pathogens), nutrient content and organic matter, comparing samples taken before and after the process. This testing has supported a successful approval of the process for treating poultry manure by the Animal and Plant Health Agency.
You can meet Lohas Recycling in person at the Horizon Europe Brokerage Event in Brussels on 26 September. Please email Lin Lianying on lian@lohasrecycling.com to arrange a meeting.
Feasibility study to optimise extraction of bio-based materials following fermentation of distillery waste with Mednet Ltd.
Pot ale is the principal effluent co-product of the whisky industry and is produced in copious quantities ,with between 8.5 -10 litres of pot ale being created for each litre of manufactured whisky. Treatment technologies have largely been restricted to applying heat to pot ale to create a molasses type syrup or energy extraction via anaerobic digestion (AD) to create heat and electricity. A Zero Waste Scotland report suggested that up to 2 billion litres of pot ale could be available for bio-refining. Laboratory research has demonstrated that a secondary fermentation process is capable of producing a valuable class of compounds known as volatile fatty acids (VFAs). Chief amongst these is hexanoic acid, a C6 short-chain acid which has numerous uses across a wide range of industries, including food, pharma, cosmetics and plastics. World supplies of hexanoic acid are largely derived from palm oil which predominantly originates from South-East Asia. The carbon footprint for world hexanoic acid production is estimated to be in excess of 37M tonnes/CO2eq. per annum.
Our work is currently in the process of identifying hexanoic acid producing bacteria from samples of AD digestate. The task is now to extend this research and undertake a feasibility study to determine how to best extract and store VFAs from a pot ale fermentation mixture using these bacteria. The results will then establish the cost profile for this element within the overall process. This is an important step in determining process optimisation and informing the financial decision to commit funds to a full sized plant.
MykoBead: an innovative and low carbon loose-fill bead insulation made from waste bio-based feedstocks with Mykor Ltd and the University of the West of England.
Mykor Ltd is a manufacturing SME established in the UK, developing cutting-edge and environmentally friendly loose-fill insulation for the building industry, and meeting a sizeable unmet need. Current building materials contribute 11% of the UK's annual carbon emissions and are unsuccessful at reducing climate change. Mykor intends to launch the first insulated bead infill created from waste bio-based feedstocks that is also low-carbon.
The goal of this project is to produce a functional, laboratory-tested prototype of the bead insulation. The eco-friendly product from Mykor aims to be high quality and reasonably priced as it's still in the development phase. The product will provide businesses with a low-carbon, fire and water-resistant solution that complies with building and carbon regulations and uses natural materials recovered from waste sources.
These awards are the first stage of a wider sustainable bio-based materials and manufacture programme being delivered by BBSRC, EPSRC and Innovate UK. The programme aims to enhance UK global competitiveness by supporting research and innovation that focuses on developing new and disruptive sustainable biomanufacturing products and processes by 2050.
Read the full UKRI press release.